Many industrial companies struggle with a problem that is barely visible but does have a major impact: negative pressure in production plants. This occurs when more air is exhausted than enters, sucking unfiltered outside air in through cracks and openings.
Negative pressure leads to drafts, temperature fluctuations, dust buildup, and ventilation disruptions. Workers experience an uncomfortable indoor environment and machinery may even malfunction. This happens despite significant investments in climate control. Many companies only realize how much money and productivity is lost when the problem gets out of hand.
Curious about what negative pressure means for your factory specifically?
The consequences of negative pressure in a factory
Negative pressure may seem harmless, but the consequences can be severe:
❌ Reduced work comfort and higher sick leave rate
Uncontrolled air currents cause drafts and temperature fluctuations, creating unsatisfied employees and an increased risk of sick leave. Research shows that an unpleasant work environment reduces productivity by as much as 15%. A cost that can easily be avoided with proper ventilation.
❌ Reduced air quality
Outside air is drawn in unfiltered, including dust, pollen and other debris. In manufacturing environments such as metalworking, this leads can lead to a dangerous accumulation of harmful particles. In the food industry, this can lead to contamination and non-compliance with HACCP standards, resulting in penalties or major recalls.
❌ Loss of production
In industries where extraction systems are used, such as laser and metalworking, negative pressure can cause machines to not operate optimally or even break down more often, and can cause unwanted temperature fluctuations.
This can add up to tens of thousands of euros per year in missed production time.
❌ Waste of energy and increased costs
Negative pressure not only draws in polluted air, but also unwanted cold in winter and uncomfortable heat in summer. This forces the climate control system to work harder, resulting in unnecessarily high energy costs.
Wasting energy is not only a cost, but also causes your business to perform less sustainably, which can affect your image and possibly non-compliance with regulations.
The biggest causes of negative pressure in factories
Wondering what causes negative pressure in your factory?
1️⃣ Poor ventilation balance
A factory with only extraction and insufficient air supply creates an imbalance of air pressure, creating negative pressure. Machines and exhaust systems often exhaust large amounts of air without sufficient fresh air supply.
2️⃣ Unstructured air supply
At the time when insufficient air supply is regulated, outside air is drawn in uncontrollably through openings, gaps or from other halls. This leads to drafts and inefficient heating or cooling. This not only causes discomfort but also increases the risk of contamination in production lines.
3️⃣ Outdated or inefficient air conditioning systems
Traditional air conditioners do not add fresh air but recirculate air. So the moment air is exhausted, negative pressure quickly develops. These air conditioners are often not designed to address negative pressure problems, so airflows are not regulated properly. We also see many heating systems that try to heat negative pressure in the winter, despite the fact that the production process releases a lot of heat that could be used instead. Many systems run at maximum capacity without really working efficiently, resulting in unnecessarily high energy bills.
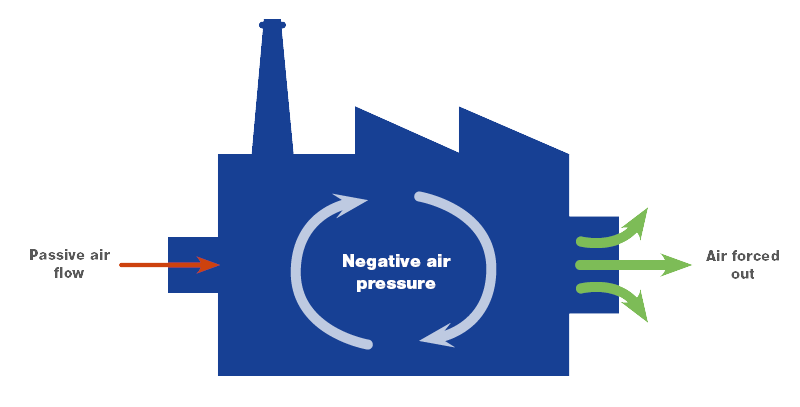
How to solve negative pressure in factories
Fortunately, there are effective ways to prevent negative pressure and create a healthy indoor environment.
✅ Well-regulated ventilation: ensure balance
The most crucial step is to restore the balance between exhaust and supply air. This can be done with mechanical supply ventilation, so there is always enough fresh air or other climate control systems that bring in controlled filtered outside air. Without a proper balance, problems such as energy loss and poor air quality continue to accumulate.
✅ Adiabatic cooling: Cooling and ventilation in one
Adiabatic cooling delivers fresh, filtered air that can be either cooled or heated, reduces drafts, and prevents negative pressure. It enhances comfort, lowers absenteeism, and reduces production downtime. Using 90% less energy, it saves on costs while promoting sustainability and a healthier, more productive work environment.
/Book%20cover%20pictures%20(whitepapers%20and%20case%20studies)/NL/247TailorSteel/247Tailorsteel_Small_NL.png?width=159&height=222&name=247Tailorsteel_Small_NL.png)
At 247TailorSteel, negative pressure was causing draft problems and inefficient climate control. Using Oxycom's two-stage adiabatic cooling, indoor temperatures were improved, suppressions eliminated, and energy consumption reduced.
✅ Result: Reduced energy costs, no negative pressure, and a pleasant and healthy working environment for employees.